Breathe in air compressor directly from the atmosphere, in order to reduce the possibility of wear, corrosion and explosion of the unit, computer room and send out an explosive, corrosive, poisonous gas, dust and other harmful substances must have a certain distance, because the compressor heat dissipating capacity is big, special machine in summer the temperature is high, so the room towards the should make between machines have good ventilation, And minimize sun exposure.
Although the compressor has a box, but it is forbidden to rain, so the compressor should not be installed in the open air. The compressor room shall be a separate building.
The compressor room must be equipped with fixed extinguishing carbon dioxide extinguishing equipment, and its manual switch must be set outside the danger zone. And always accessible. Fire extinguishing equipment Carbon dioxide fire extinguisher or powder fire extinguisher should be placed near the protected object, but should be outside the danger zone.
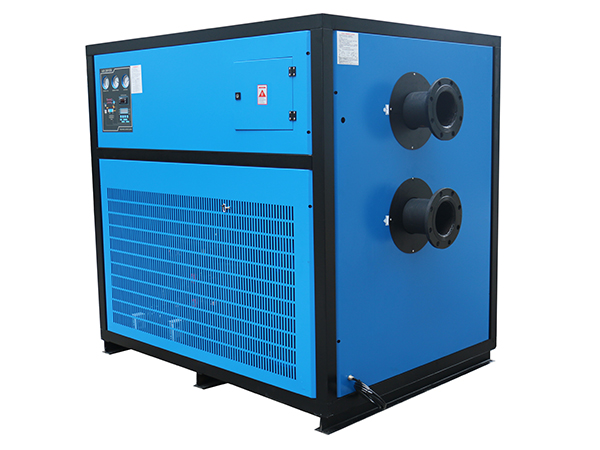
Equipment room installation requirements
The floor should be smooth cement, and the inner surface of the walls should be white. The compressor base should be placed on the concrete floor, and the plane levelness should not be greater than 0.5/1000 mm. And there are grooves around 200mm away from the unit, so that when the unit stops for oil change, maintenance or washing and cleaning the ground, oil and water can flow away from the groove, and the groove size is determined by the user. When the compressor unit is placed on the ground, it should be ensured that the bottom of the box fits well with the ground to prevent vibration and increase noise. To the user with conditions, the wall of the machine room can be affixed with a sound-absorbing board, which can further reduce the noise, but it is not suitable to use hard surface materials such as ceramic tiles to decorate the wall. The air-cooled compressor is greatly affected by the ambient temperature. Therefore, the ventilation in the equipment room must be good and dry. The heat exchange air can be led out of the air duct or an exhaust fan can be installed to control the ambient temperature of the compressor within -5 ° C to 40 ° C. The temperature in the equipment room should be above 0 ° C. There is little dust in the machine room, the air is clean and free from harmful gases and corrosive media such as sulphuric acid. Depending on the nature of the product processed by your company, the air inlet should be equipped with a primary filter. Effective window circulation area should be greater than 3 square meters.
Power supply and peripheral wiring requirements
The main power supply of the compressor is AC(380V/50Hz) three-phase, and that of the freeze dryer is AC(220V/ 50Hz). Confirm the power supply.
Voltage drop shall not exceed 5% of rated voltage, and voltage difference between phases shall be within 3%.
Compressor power supply must be equipped with isolation switch to prevent short circuit phase loss operation.
Check the secondary circuit fuse and select the appropriate fuse - free switch according to the power of the compressor.
The compressor is best to use a set of power system alone, to avoid parallel use with other different power consumption systems, especially when the power of the compressor may be large due to excessive voltage drop or three-phase current imbalance and the formation of compressor overload protection device action jump. Must be grounded to prevent leakage caused by danger, must not be connected to the air delivery pipe or cooling water pipe.
Requirements for pipeline installation
The air supply port of the unit has a threaded pipe, which can be connected with your air supply pipeline. Please refer to the factory manual for installation dimensions.
In order to avoid affecting the operation of the whole station or other units during maintenance, and to reliably prevent the backflow of compressed air during maintenance, a cut-off valve must be installed between the unit and the gas storage tank. In order to avoid affecting gas consumption during filter maintenance, standby pipelines should be set in the pipeline of each filter, and feeder pipelines must be connected from the top of the main road to avoid the condensate water in the pipeline flowing down to the compressor unit. Shorten the pipeline as far as possible and straight line, reduce elbow and all kinds of valves to reduce pressure loss.
The connection and layout of air pipelines
The main pipe of compressed air is 4 inches, and the branch pipe should use the existing pipe as far as possible. The pipeline should generally have a slope greater than 2/1000, the low end of the sewage valve (plug), the pipeline should be less bending short straight valve as far as possible. When the underground pipeline passes through the main road surface, the buried depth of the top of the pipe is not less than 0.7m, and the secondary road surface is not less than 0.4m. The installation position of the pressure and flow meter and its surface size should enable the operator to see the indicated pressure clearly, and the pressure class scale range should make the working pressure in 1/2 ~ 2/3 position of the dial scale. Pressure strength and air tightness test should be done after the installation of the system, not hydraulic test. 1.2 ~ 1.5 times the pressure of the same gas, leakage is qualified.
The anti-corrosion of air pipeline
After installation is finished, try to press qualified, after clearing the dirt of the surface, bilge, rust spot, welding slag, it is anticorrosive processing with besmear paint. Pipeline paint has anti-corrosion, prolong the service life of the pipeline, but also easy to identify and beautiful. Generally, the surface is coated with anti-rust paint, and the specified blend paint is applied.
Air pipeline lightning protection
Once the high voltage induced by lightning is introduced into the workshop pipeline system and gas equipment, it will cause personal safety accidents of equipment. So the pipeline should be well grounded before entering the workshop.
Pipeline pressure loss
When the gas flows in the pipe, friction resistance is generated in the straight pipe section. Local resistance in valves, tees, elbows, reducer, etc., resulting in gas pressure loss.
Note: the total pressure drop of the pipeline part shall also include the partial pressure loss caused by elbows, reducing nozzles, tee joints, valves, etc. These values can be checked from the relevant manual.
Ventilation of the compressor air pressure system
Whether the user uses an oil-free machine or an oiler, or whether the user uses an air-cooled compressor or a water-cooled compressor, the ventilation problem of the air compressor room must be solved. According to our past experience, more than 50% of the faults of air compressors are due to the neglect or wrong understanding of this aspect.
In the process of the compressed air will have a lot of heat, and if this heat cannot discharge air compressor room, in a timely manner will result in the temperature of air compressor room gradually rise, so the temperature of the air compressor suction mouth will more and more high, so a vicious circle will cause high discharge temperature of compressor and alarm, at the same time because of the high temperature air density is small and will cause gas production reduced.
Post time: Jul-06-2022